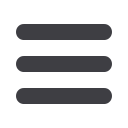
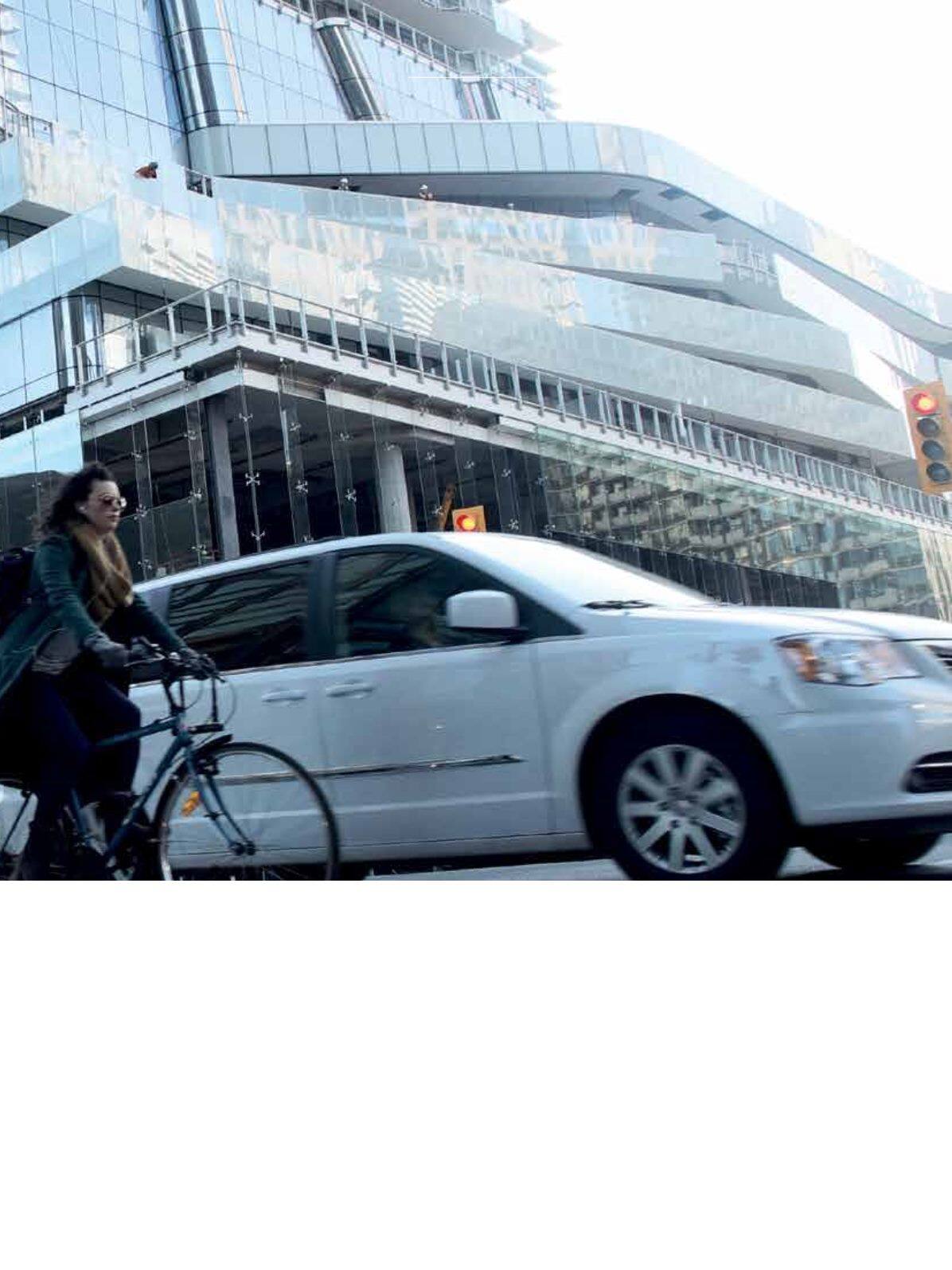
feature
PHOTO
SAMI VÄLIKANGAS
project, the latest BIM models now integrate the fourth
dimension: time. This allows planners to properly schedule
each of the individual works to be carried out during
construction, anticipating roadblocks and conflicts that
might result in costly delays. “By sequencing those trades in
the most optimal manner, you can actually reduce the time
it takes to build a building,” Wash says.
“KONE is working with architects on next-generation
toolboxes that have innovative BIM models at their core
to not only let them understand the future capabilities of
our elevators, which are getting more sophisticated and
smarter, but also how to actually construct the building,”
he adds.
A high-profile example of this cooperation is One Bloor,
a 70-story, mixed-use retail and residential building in the
heart of Toronto. KONE provided the elevator ‘objects’ used
in the BIM model. “We used BIM with the contractor to
accelerate the design and the sequencing of the trades,”
Wash says.
Meanwhile, the building process is also getting a boost
from smart innovations like KONE UltraRope (a carbon-fiber
elevator rope that replaces the steel rope traditionally used
for elevators) and KONE JumpLift (a construction elevator
that uses the building’s internal hoist and runs at speeds
that are two to three times that of an old-fashioned outside
hoist). For tall buildings in particular, these innovations can
lead to substantial energy savings from eliminating tons of
steel from the load equation, and productivity gains of one
to two hours per worker per day, as personnel won’t be
waiting so long for a ride.
17