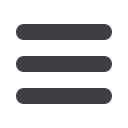
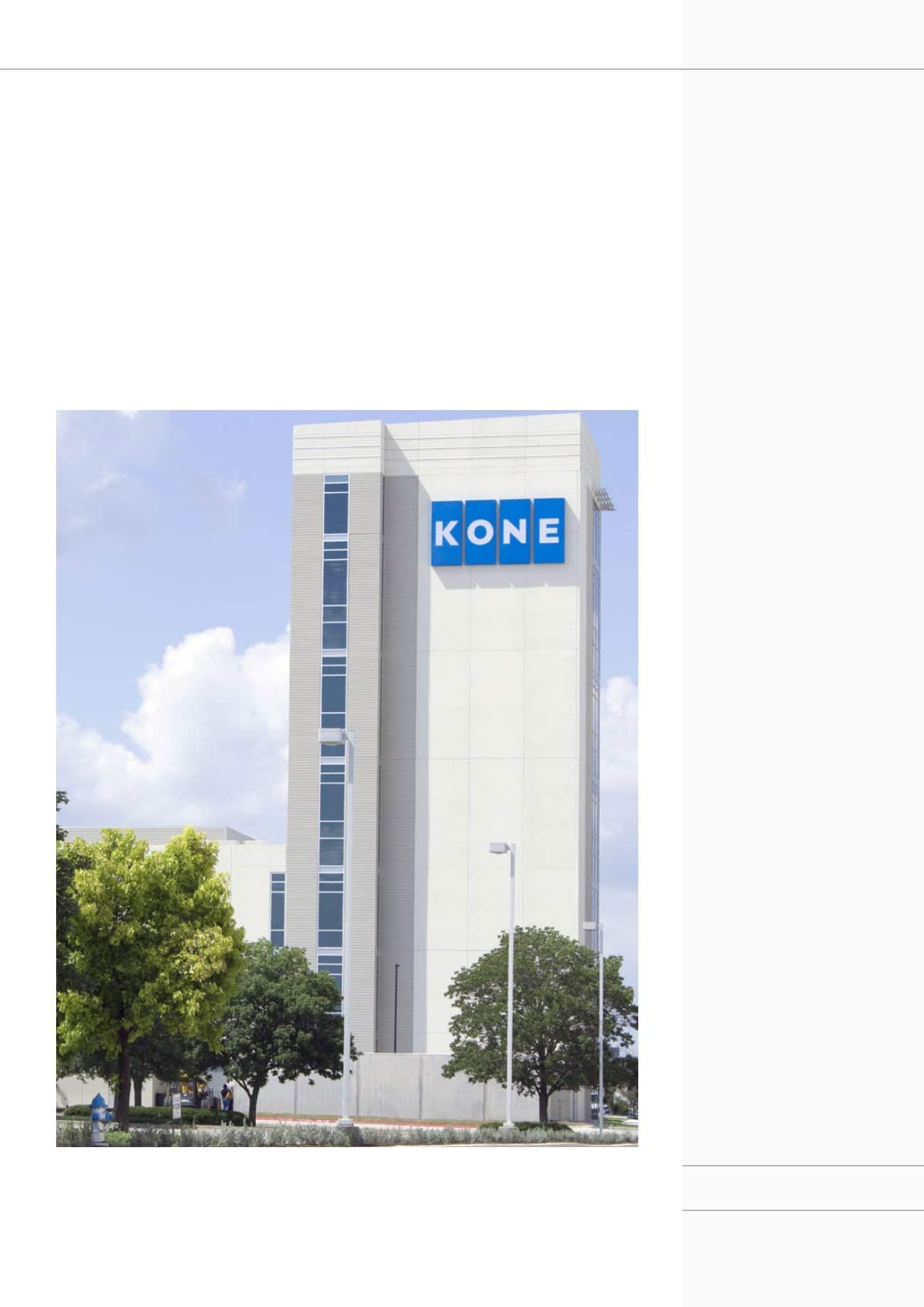
KONE 2016 | SUSTAINABILITY REPORT
SUPPLY CHAIN
4 5
Read more
about our logistics on p. 19.
implement the 5S* method in our offices,
factories, installation sites, and distribution
centers. Furthermore, we have developed a
Lean manual and a management model of
continuous improvement in implementing
these principles. Another new development is
the establishment of Lean capability teams on
a global level.
KAIZEN ACTIVITIES TO IMPROVE
THE USE OF PACKAGING
MATERIALS
KONE organized Kaizen activities
in 2016 to think of ways to reduce
packaging in our deliveries and speed
up installation at construction sites.
Currently the components found
inside packages and containers are
not fully arranged in the order the
installer needs them when unpacking
materials on-site and installing the
elevator. The packaging materials also
take up additional space both during
transportation and on-site, increasing
emissions and costs.
To inspire out-of-the-box ideas, the
workshop participants were from
different KONE units. The team came
up with lots of innovative suggestions
on how to reduce the amount of
packaging materials needed and to
make them more environmentally
sustainable. For example, participants
recommended using the car panels as
part of the packaging, removing “box
in a box” packaging. The ideas have
already been tested in the field.
Kaizen philosophy involves everyone
in making practical improvements. It
is an integral part of the way we work
at KONE.
A large number of employees gained new
capabilities when they received Kaizen training
as part of Kaizen events.
More than 800 Lean and Six Sigma projects
were completed successfully in 2016. To date,
hundreds of KONE employees have qualified as
Six Sigma Green Belts and Black Belts.
KONE’s new facility in Allen, Texas features a test tower for evaluating prototypes and new components before
they go into production.
*The name of the 5S methodology comes from the words sort, stabilize, shine, standardize, and sustain.